Everything You Need to Know About 3D Surface Modeling
The realms of engineering and 3D designs are fascinating and intricate, wherein 3D surface modeling is pivotal. This 3D design representation approach allows professionals to achieve a high level of precision and accuracy. It also enables engineers to facilitate an efficient design process by thoroughly analyzing and modifying the design before final construction.
If you want to learn more about this vital engineering element, give this article a read. It will give you a comprehensive understanding of what surface modeling technique is, where it is mostly used, and what its pros and cons are. Let’s begin!
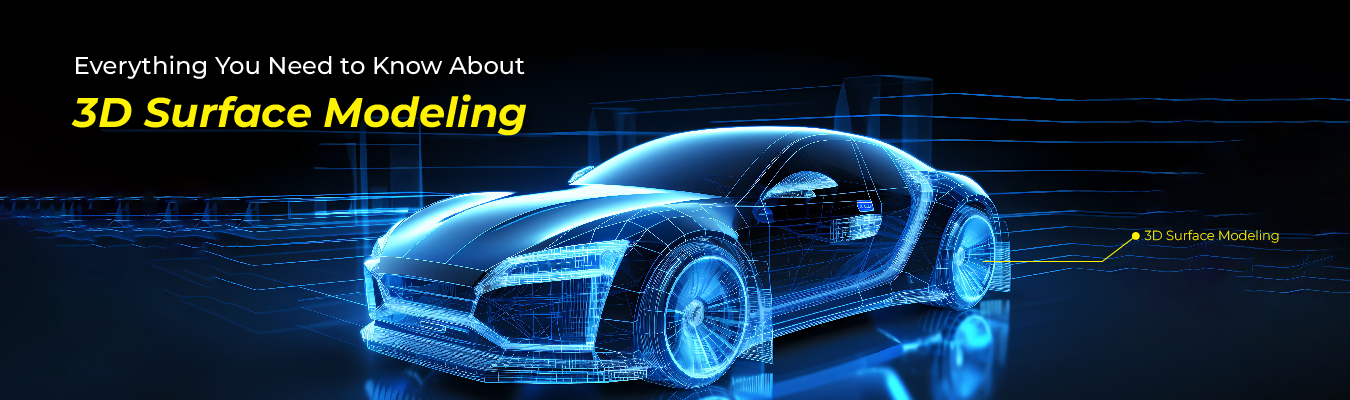
What is surface 3D modeling technique?
The surface 3D modeling technique is a computer-generated process where an accurate mathematical representation of a surface is developed. With this 3D modeling process, shapes that are hard to visualize, design, or animate, can be represented ideally for designing purposes. The external facets or features of an object, the edges, etc., are depicted through the surface models. Also, surface models are inherently hollow from the inside since designers only focus on the exteriors of the object.
In simple words, surface modeling helps 3D modelers create complex shapes defining the surface features. The process is done through advanced CAD software that extends a surface over a physical object with 3D curves. This modeling technique is ideally used for animation, automotive design and development, computer video game design, architecture, advertising, and the like. In some TV commercials of luxury cars, the smooth surfaces of the vehicles are often created through the surface modeling method.
Where is surface modeling mainly used?
Since the technique mainly represents the boundaries of an object’s surface, modelers get a higher degree of control over the design’s aesthetics. That’s the reason surface modeling is commonly used to visualize mechanical objects and organic shapes that usually require a greater level of detail. Models that have unique features, unreal geometries, or weird shapes and thicknesses, are developed using this modeling procedure.
The technique is a free-form style of CAD modeling where the curves and corners can be tweaked and reshaped per the designer’s creative thoughts. Let’s discuss the several business sectors wherein surface models are commonly applicable.
The AEC (architecture, engineering, and construction) industry primarily leverages this technique. In this industry, accurate, realistic visualization of proposed constructions and buildings is the main criterion. Surface models help create realistic architectural renderings and develop accurate surface data of what the final construction will look like. Hence, most modern architectural projects resort to this 3D design method.
Next is the aerospace industry, where design architects leverage this modeling approach to develop complex curvatures. They can also develop free-flowing aerodynamic shapes, aircraft fuselages, thin-walled structures, etc.
The automobile design and development sector also utilizes surface model designs to develop Class A surfaces. Automotive designers require efficient curve networks and smooth surface patches to represent complicated automotive curvatures in digital forms. This is only possible in surface 3D designing technique.
Surface models are also crucial for modern medical imaging, pathological deviations, and three-dimensional structures. Medical researchers, doctors, and surgeons can easily track and analyze diseases and experiment with various treatment outcomes. Simulation features that help researchers visualize patient diagnoses and different scenarios can be added to the renders.
What do you understand by hard surface modeling?
3D hard-surface modeling is a surface modeling process for developing non-living objects having hard surfaces. Inanimate objects like weapons, fictional machines, computers, buildings, and automobiles with static surfaces are best represented with this technique. This approach is defined by an object’s geometry and surfaces and is crucial to visualize any man-made artificial objects’ exteriors along with VFX.
Organic modeling is another approach to surface modeling that is the stark opposite of hard-surface modeling. This modeling technique focuses generally on living objects such as characters, animals, plants, etc.
How are solid modeling and surface modeling different from each other?
Solid modeling and surface modeling are two distinct 3D modeling approaches to 3D computer-aided design and computer-aided manufacturing. Each has its own strengths and applications. Based on the project requirements, 3D modelers select any one of the two methods to achieve the desired outcomes.
In solid modeling, the models are represented as complete 3D volumes with mass, density, and volume. These models have surfaces with defined spaces and are comprised of complex shapes and primitives, like cylinders, cubes, spheres, etc. The process of model creation happens through a sequential set of additive and subtractive operations. This technique is perfect for developing geometrically accurate and defined objects having calculable volume.
Whereas, surface modeling showcases physical objects with complex organic shapes and forms. Surface 3D models are developed through techniques like sweeping, lofting, patching, blending, etc. Unlike 3D solid modeling, which defines the interior of an object, surface modeling focuses completely on the external features and boundaries or surfaces. The differences between solid modeling and surface 3D modeling make each of the techniques unique at its own merit.
Different types of surface modeling
There are different types of surface modeling techniques used to represent external surfaces and boundaries of objects. Specialized CAD software are there for the purposes often utilized by professional 3D modeling services providers. Check out some of these variations.
- Primitive-based modeling
- Curve-based modeling
- Free-form modeling
- Patch-based modeling
- Feature-based modeling
Each of the above techniques of creating surface models has its own characteristics. Professional 3D modelers usually choose a mix of these procedures based on the project requirements, level of expertise, as well as availability of the required software.
Advantages and disadvantages of surface modeling
The process meets several engineering design requirements thanks to its unprecedented flexibility. The main advantage production designers enjoy is bringing futuristic imagination to reality, capturing complex geometries with precision.
However, nothing comes without some disadvantages or cons. Let’s discuss the pros and cons of surface 3D modeling for design engineering.
Advantages:
More free-form shapes and life-like organic shapes could be created with surface modeling.
Owing to the technique’s flexibility, complex surfaces can also be easily created, unlike other modeling techniques.
It has become a pivotal tool for creating accurately realistic models of physical objects. Which is why this 3D design method is often used for creating video game characters.
The process is definitive without any ambiguity.
The extremely malleable nature of this technique makes it ideal for creating ergonomic medical implants for the human-body, such as prosthetic limbs, dental implants, etc.
However, as mentioned, surface models also have certain limitations and disadvantages. Let’s check some of them out.
Disadvantages:
Surface modeling is not parametric; that is., the models are not defined by any solid parameters. This makes any design iteration challenging.
Extensive technical knowledge and expertise regarding modeling is required since model creation is rather complex.
Owing to the complexity, the time taken is also longer than other modeling methods.
The surface models have higher file sizes and thus require large storage space.
Final thoughts
To conclude, 3D surface modeling is an invaluable tool for modern engineering design creations with great control of aesthetics. When used in combination with other modeling procedures, incredibly complex 3D models can be created. With such hybrid modeling methods, advanced medical 3D designs, engineering elements, and more are made possible.
It is extremely important for any aspiring 3D professional to master surface modeling. Several 3D modeling software are there for the process that have a simple interface and easy learning curve. These high-end software offer free-form modeling, surface-blending, real-time surface diagnostics, and more. Trained professionals leverage these cutting-edge tools.
Hence, it is always recommended to hire expert 3D design services providers for all 3D CAD design requirements. Contact such a professional company and grow your business to new levels.